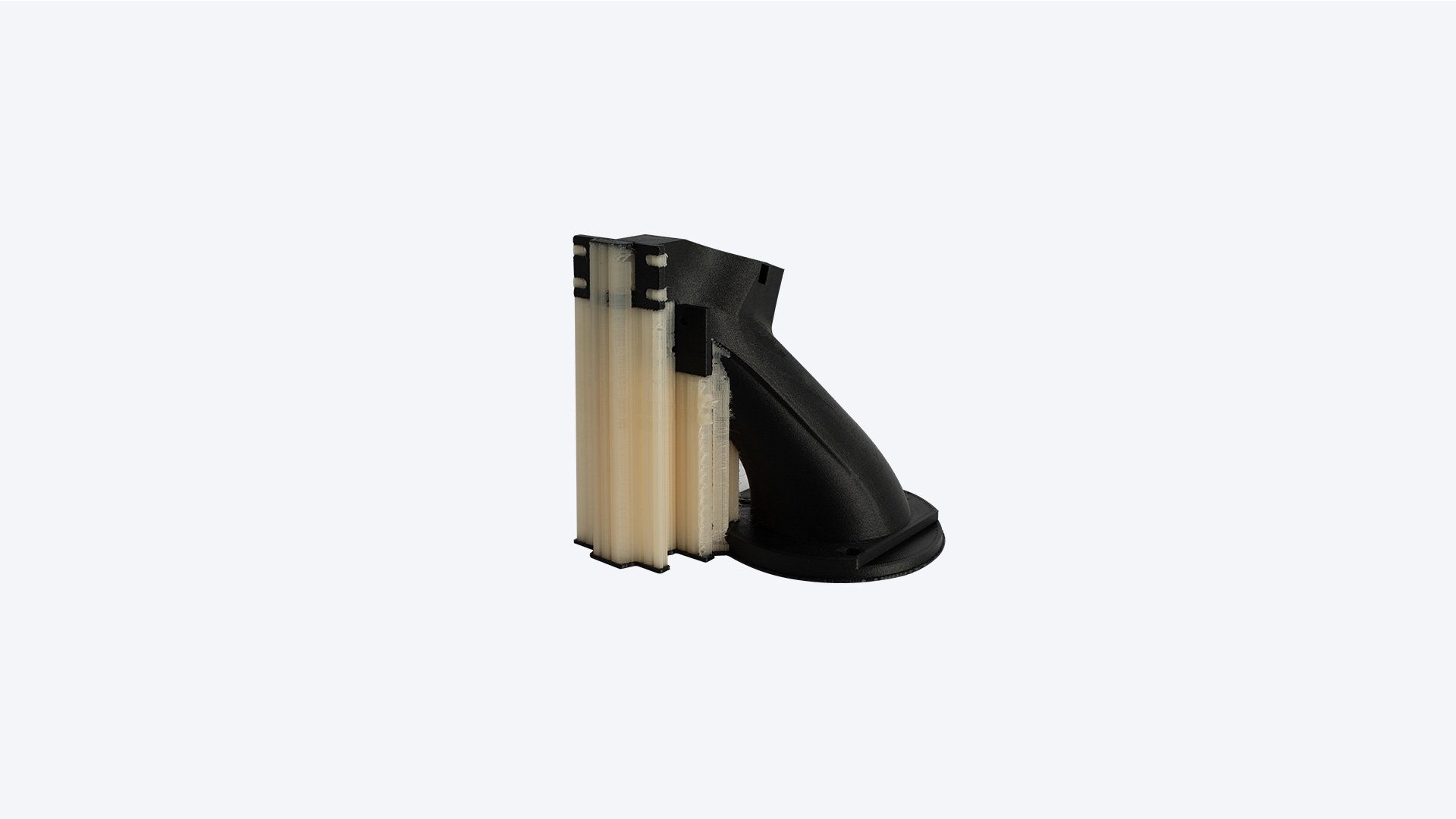
ARGO 500 HYPERSPEED is the new solution engineered by Roboze to meet the needs of the most demanding industries. In this context, we conducted a detailed simulation to compare the performance of the new ARGO 500 HYPERSPEED printer with the previous model, ARGO 500. Using a hopper as a case study, the simulation involved the composite Carbon PA PRO as the main material and KRONOS S1, a water-soluble support material. The goal was to evaluate the differences in terms of printing time, material waste, annual productivity, and maintenance times. The collected data provides a clear picture of the potential of the new ARGO 500 HYPERSPEED technology compared to the previous model.
Simulation conducted on a single job under the same conditions
Comparing the new ARGO 500 HYPERSPEED with the previous ARGO 500, the data is clear:
• Printing Time: The new ARGO 500 HYPERSPEED reduces printing time from 26 hours to just 16 hours. This represents a significant improvement in production speed, saving valuable working hours for each piece produced.
• Material Waste: Another crucial aspect is the reduction in waste. The ARGO 500 HYPERSPEED generates only 119 grams of material waste compared to 748 grams with the previous version. This not only reduces production costs but also makes the process more environmentally sustainable.
These results stem from an innovative element, currently patent-pending, that the Roboze team has named Smart Gcode. This advancement is based on new software algorithms that, combined with the performance of the new hardware, the PolyFlowX system, also patent-pending, ensure a reduction in dual extruder printing times by up to 92% compared to the previous version. This optimization is achieved by improving all movements and paths and completely eliminating idle times during the extruder change process, a problem currently present in all other systems.
Simulation of an Annual Production Cycle
To better understand the impact of these improvements, we simulated an annual production cycle of the hopper. The results are impressive:
• Productivity: The ARGO 500 HYPERSPEED allows the production of 422 parts per year compared to 260 parts with the previous version, increasing productivity by 62%.
• Material Savings: The percentage of auxiliary material required decreases from 12% to 7.5%, resulting in a saving of 4.4%.
• Maintenance Time: The new machine requires significantly less maintenance, reducing annual maintenance time from 117 hours to 41 hours, a 65% reduction.
Annual Cycle | ARGO 500 | ARGO 500 HyperSpeed | Δ (%) |
Number of printed parts | 260 | 422 | +62 |
Auxiliary material (%) | 12 | 7,5 | -4,4 |
Maintenance time (h) | 117 | 41 | -65 |
The adoption of the ARGO 500 HYPERSPEED represents a crucial step forward for companies looking to improve their production efficiency and reduce operating costs. The benefits observed in the hopper case study clearly demonstrate how this technology can revolutionize additive manufacturing, offering tangible advantages in terms of time, materials, and maintenance.
If you want to learn more about how ARGO 500 HYPERSPEED can transform your production, contact us today. Roboze continues to innovate to provide you with cutting-edge 3D printing solutions that meet the needs of the modern market.