PEEK, a revolutionary material for industrial 3D printing
Why choose PEEK for your business?
- Geometric freedom at high temperatures
- Metal replacement in corrosive environments
- Combination of lightness and mechanical resistance
Ask our experts about PEEK and revolutionize your production with Roboze superpolymers
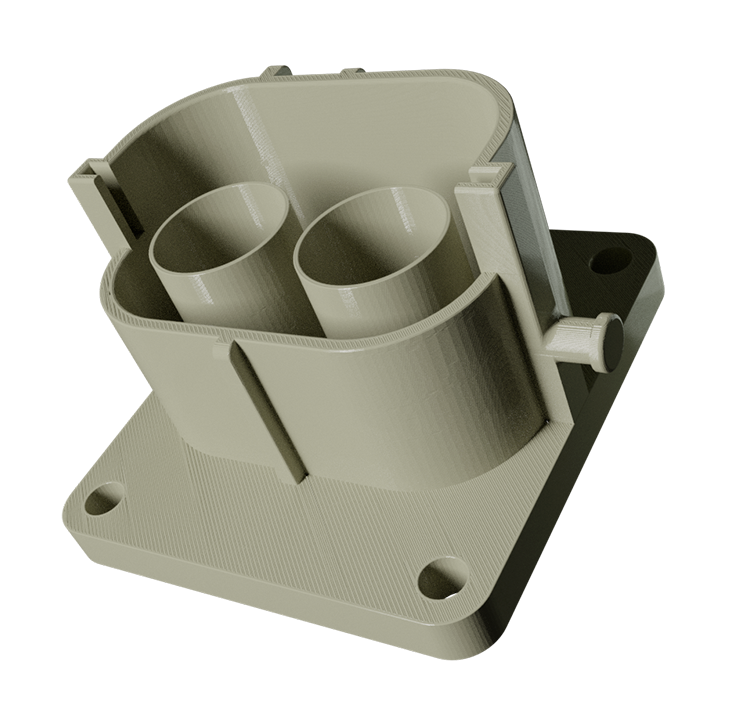
PEEK, a new opportunity for metal replacement in extreme environments
Polyether ether ketone (PEEK) is a high performance semi-crystalline organic thermoplastic polymer belonging to the polyaryletherketone (PAEK) family.
The combination of mechanical strength, high temperature resistance, and chemical resistance of PEEK make it the material of choice for environments with difficult working conditions.
PEEK unique properties
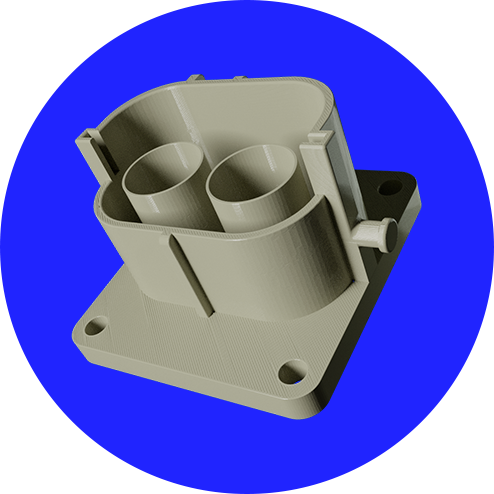
Fatigue resistance
PEEK has a very high fatigue strength. This feature makes it perfect for tribological applications where wear resistance and self-lubricating properties are required. Roboze customers use this material for functional prototyping, small series production and one-off products subjected to extreme conditions.
Heat resistance
From a thermal point of view, PEEK has excellent dimensional stability and a CUT of 473°F (245 ° C). These properties result in PEEK being able to withstand heavy loads for long periods at a high temperature without permanent deformation.
Chemical Inertia
From a chemical point of view, the tests carried out demonstrate chemical inertia to most organic solvents, acids and bases. This makes it suitable for environments with critical conditions such as naval and Oil & Gas. In the medical field, the printed parts can be sterilized with saturated steam, ethylene oxide, hydrogen peroxide and peracetic acid solution.
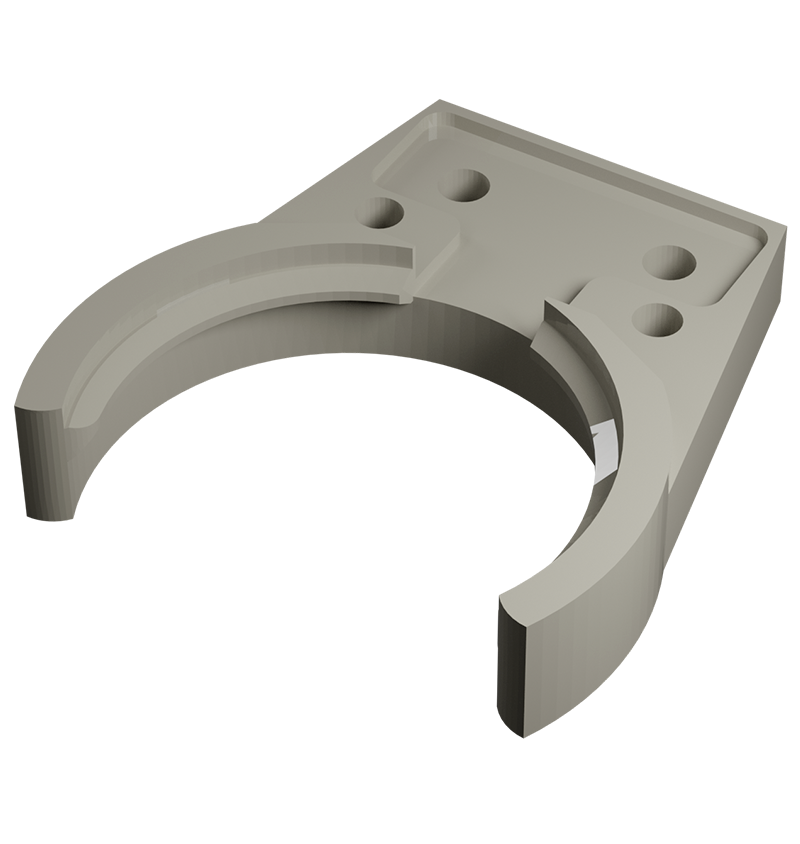
What are the benefits of PEEK?
- Resistance to chemicals, wear, fatigue and sliding
- Mechanical properties superior to other thermoplastic polymers
- It maintains unaltered mechanical properties up to 302°F / 150°C (Tg, Glass Transition Temperature) and can be used at temperatures up to 482°F / 250°C (Continuous Use Temperature)
- It contains no known toxic chemicals, is a flame retardant (UL94 V0) and a material that complies with FTS (flame, smoke, toxicity) levels
- The excellent thermal and electrical insulation properties of PEEK make it ideal for electronic applications
Why you should print in PEEK with Roboze?
Roboze printing solutions have been designed to produce finished parts using the best performing super polymers and composites in the entire industry. Roboze monitors the management of the material, from hygroscopic control to drying and preheating, up to the gradual cooling phase of the produced part, thus maximizing the crystallinity of the PEEK print. The Roboze Automate technological ecosystem, integrated into Production solutions, brings industrial automation to 3D printing allowing total process control, repeatability, and accuracy comparable to any other industrial production process.
Applications and Industries
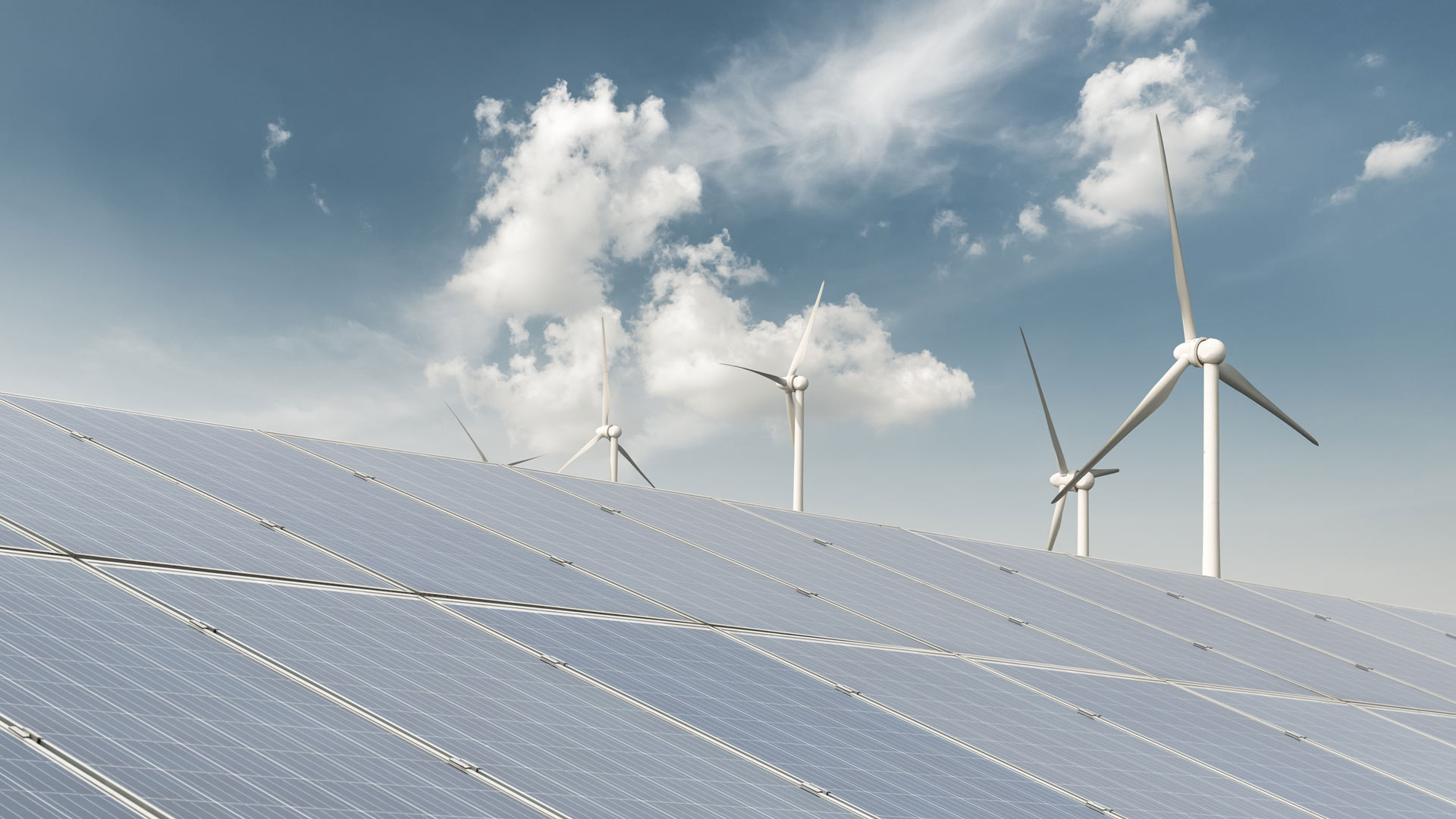
PEEK for the energy sector
PEEK is an ideal candidate to support metal replacement in the energy sector thanks to its high resistance to chemicals and temperatures.
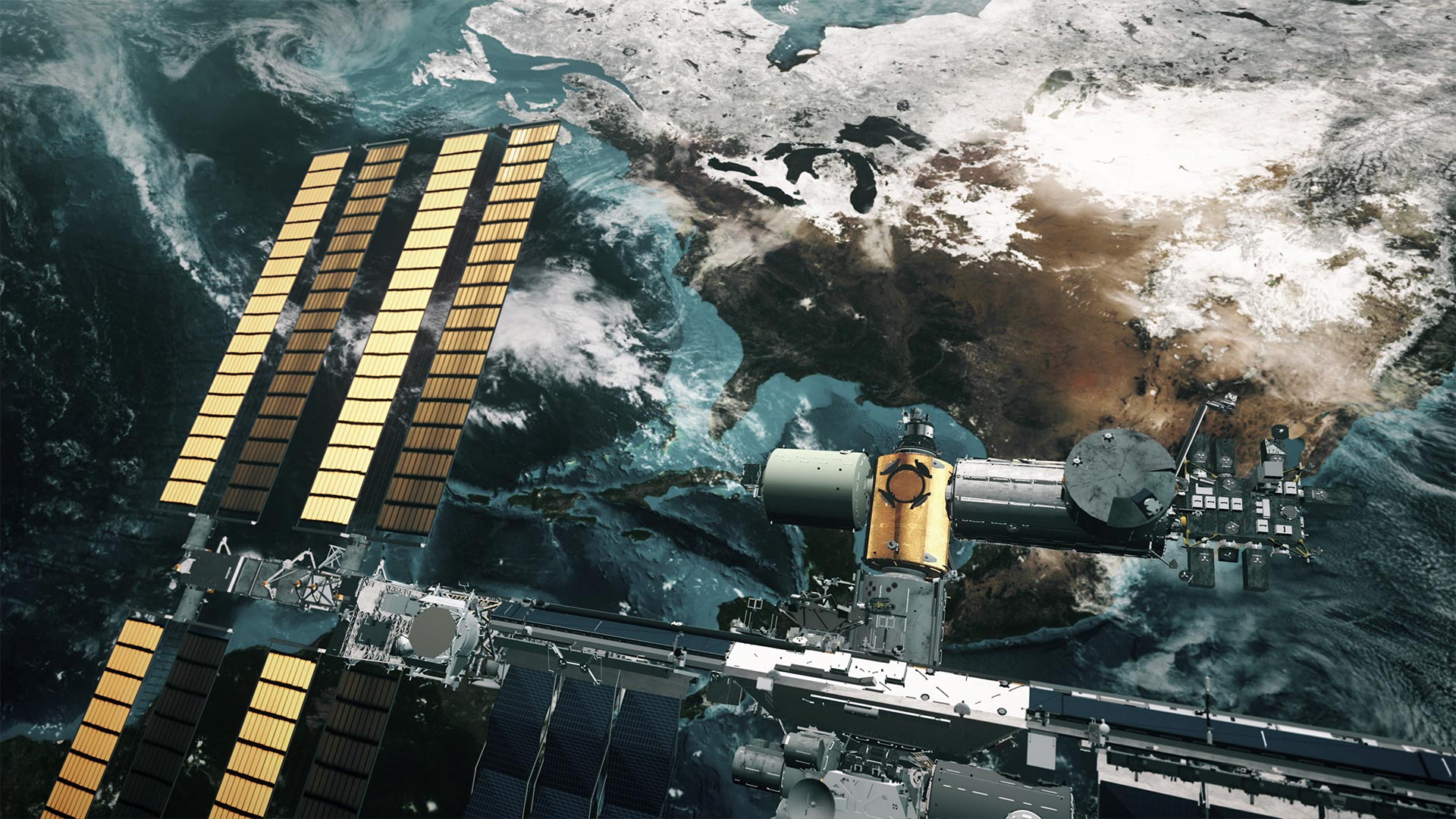
PEEK for Aerospace & Defense
Being a polymer with properties similar to metal, PEEK allows significant weight reduction with a consequent decrease of fuel consumed and emissions released, as well as flexibility of the production process and complex geometries possible through Additive Manufacturing.
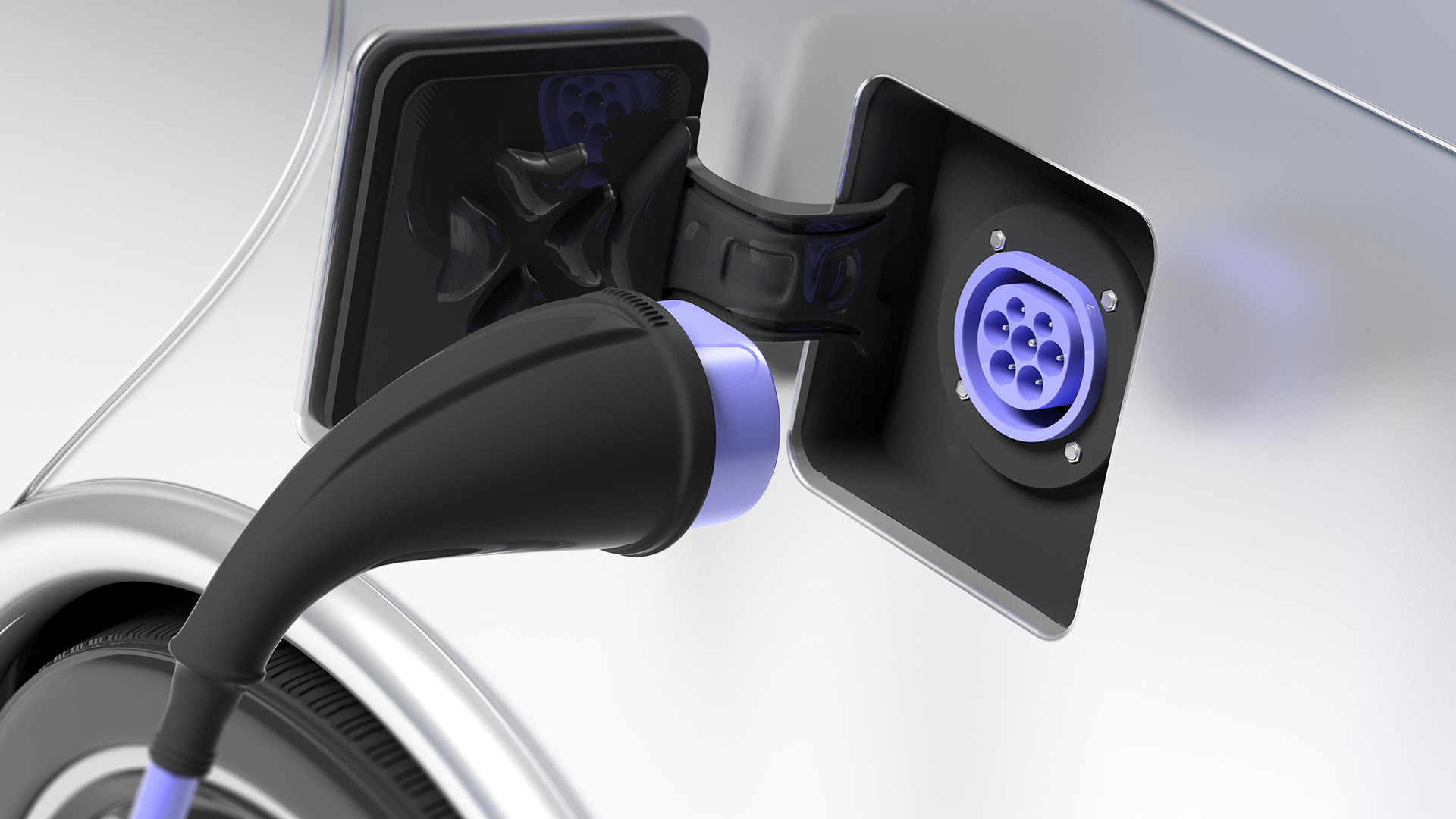
PEEK for Mobility & Trasportation
With the use of materials such as PEEK being resistant to extreme conditions, the efficiency of mobility is improved, reducing costs, and producing just in time while supporting the companies that build the future of transport every day.
They have already chosen Roboze
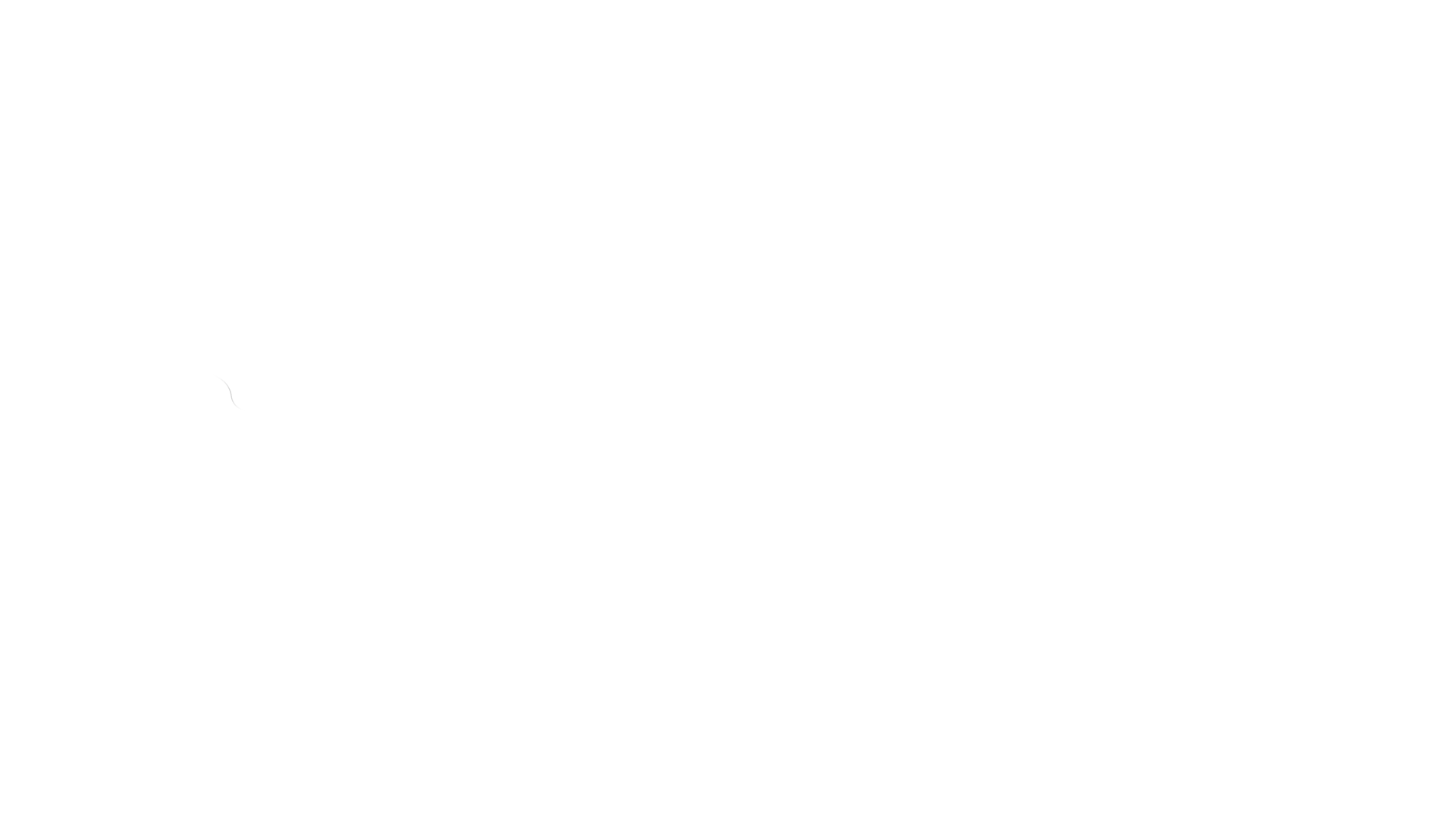
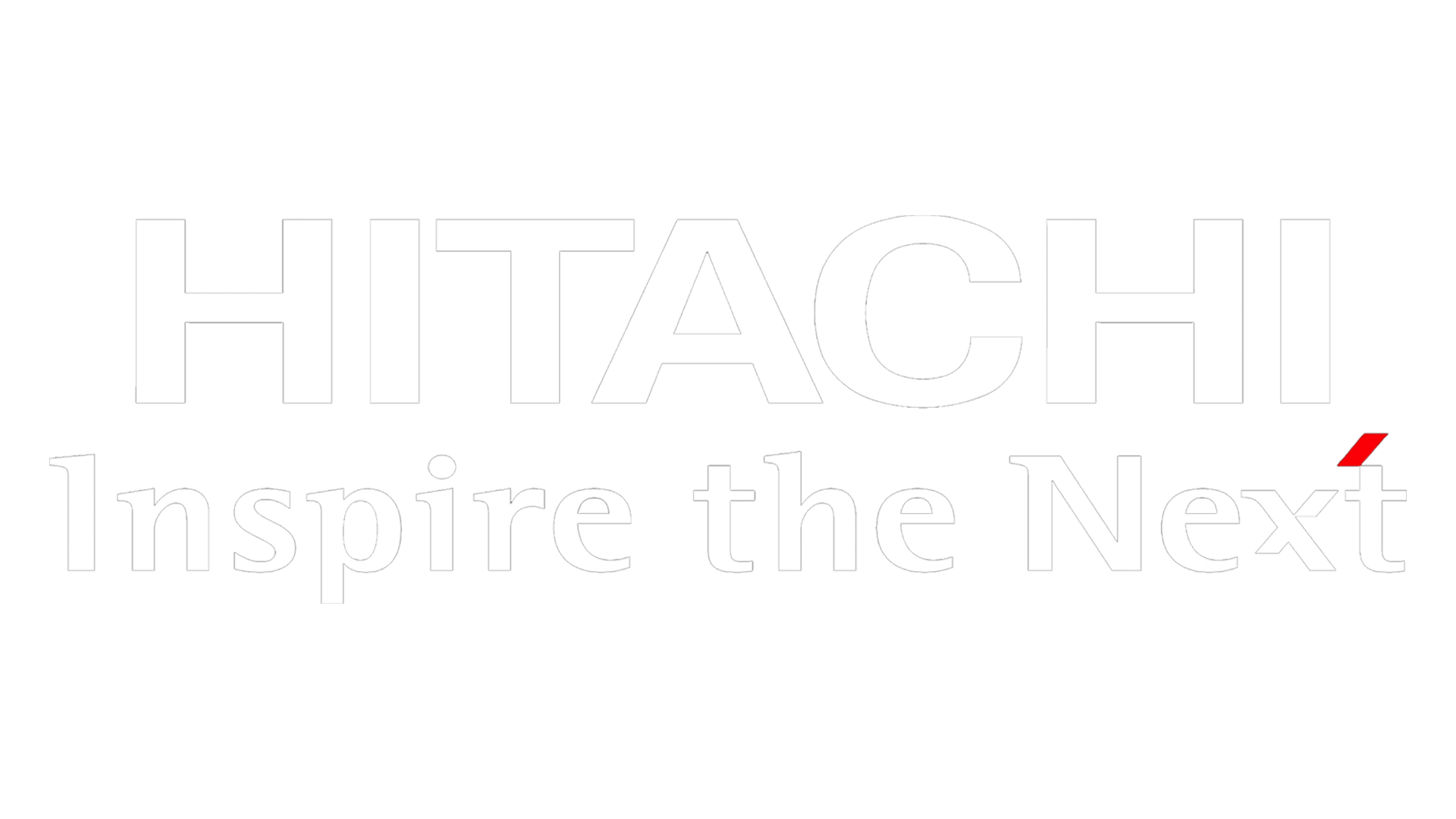
Print with the ARGO 500
The Roboze ARGO 500 is the first 3D printer for large format superpolymers in industrial production. The mechanical properties and dimensional tolerance of the manufactured parts pass through perfect temperature management during the entire process. The thermal melting of the layers is the result of extrusion temperatures up to 842° F (450 ° C), inside a hot working chamber heated up to 356 ° F (180 ° C), to guarantee the perfect fusion of the layers with a dramatic increase in the mechanical properties of the components products.
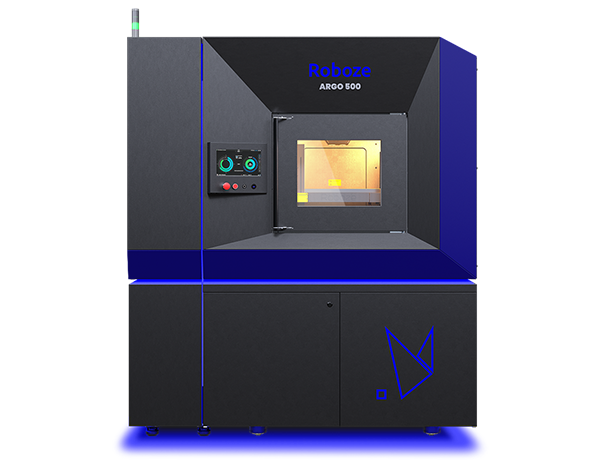
Without a heated chamber:
- molded PEEK would have a low crystallinity rate and shrinkage would be uncontrollable
- an additional heat treatment process called annealing would be necessary
Utilizing the heated chamber printing with the ARGO 500:
- guarantees better properties of the polymers and high precision of the printed part
- does not require further heat treatments
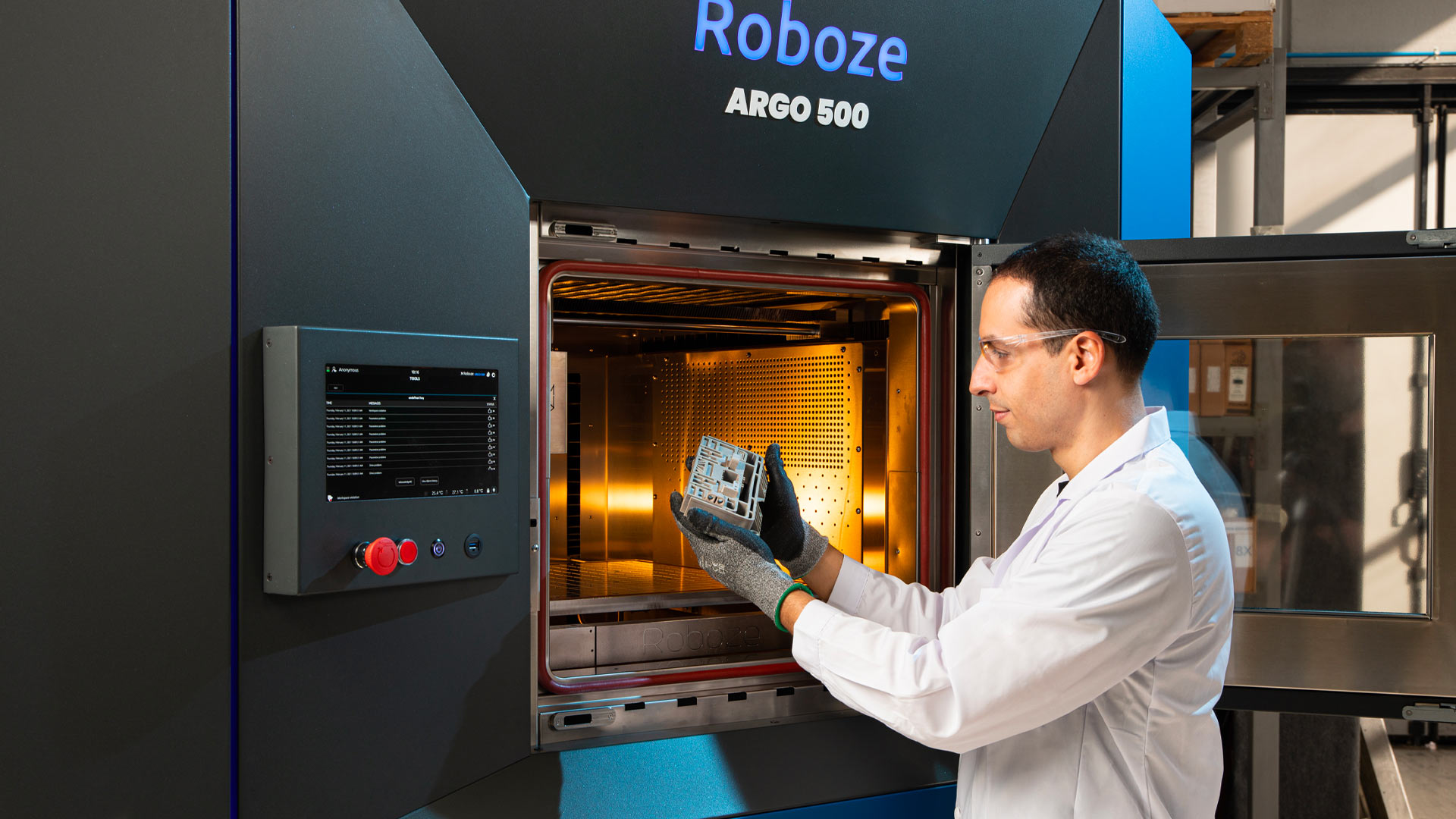
Repeatable, automated, and controlled printing
ARGO 500 is the first 3D printer for super polymers and composites equipped with the Roboze Automate technological ecosystem, which brings industrial automation to 3D printing. Thanks to the combination of hardware, advanced sensors, B&R PLC control, Roboze Beltless technology, and total process control, Roboze 3D printing is repeatable, automated, and controlled like any other industrial production process.
Who is Roboze?
Roboze designs and manufactures the world's most accurate 3D printers to produce parts with composite materials and super polymers that replace metals in industries with extreme working conditions. The main objective is to shape a new paradigm in digital production through a complete range of advanced 3D printers developed with the collaboration of the world’s best players, bringing Additive Manufacturing closer to the standards of traditional production.
Through its global network of manufacturing as a service with the production of one-demand and just in time parts, the Roboze 3D Parts division allows companies to reduce costs and time by shortening the steps of their supply chain and digitizing their inventory.